A Beginner’s Guide to Butchery Equipment Maintenance
Crucial Tips for Picking the Right Butchery Devices for Your Organization
Selecting the right butchery devices is crucial for any company in the meat market. It needs a cautious assessment of different variables that can influence performance and security. Top quality, toughness, and conformity with guidelines play considerable duties in this decision-making procedure. Understanding just how to examine these elements can set an organization in addition to its competitors. What factors to consider should be focused on to assure peak performance and protection for personnel?
Examine Your Service Demands

Prioritize Top Quality and Toughness
Picking butchery tools requires a strong focus on top quality and sturdiness, as these aspects directly influence long-lasting operational success. High-quality equipment not only boosts efficiency however likewise guarantees consistent efficiency, decreasing the likelihood of breakdowns that can interfere with solution - Butchery Equipment. Resilience is important, especially in a requiring environment where devices and makers encounter daily wear and tear.Investing in sound equipment can cause significant price financial savings over time, as durable products tend to require much less frequent replacement and repair work. In addition, top-tier products can endure the rigors of heavy use, maintaining their capability and appearance over extensive periods.When examining options, it is advisable to take right into account trustworthy brand names known for their commitment to quality. Checking out client testimonials and looking for suggestions from industry peers can give insights into the integrity of specific tools. Inevitably, focusing on quality and toughness will certainly contribute to a much more lasting and effective butchery procedure
Think About Security Qualities
Many security features should be focused on when picking butchery tools to ensure a protected workplace. Devices must ideally have safety guards to avoid injuries throughout operation. Additionally, automated shut-off mechanisms can improve safety and security by immediately stopping devices function when a breakdown is discovered. Non-slip surface areas on workstations and cutting areas additionally help decrease the danger of accidents.Moreover, ergonomically developed tools can decrease the physical pressure on workers, decreasing the likelihood of injuries gradually. It is vital to review the materials utilized in the tools; stainless-steel alternatives are not just resilient however additionally simpler to clean, decreasing the danger of contamination.Furthermore, proper labeling of tools and clear operational manuals can help workers in comprehending security procedures. Inevitably, prioritizing these security includes not just shields employees however additionally adds to an extra effective and certified butchery procedure.
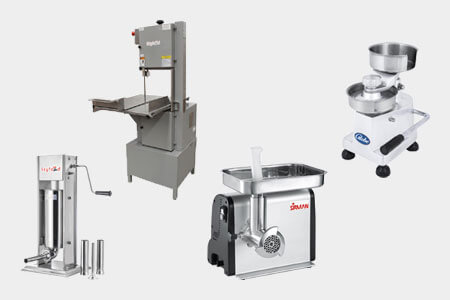
Review Area and Format
Reviewing space and format is important for a reliable butchery operation. By identifying the offered space, one can enhance the process style to enhance efficiency. This strategic preparation warranties that tools placement assists in smooth motion and task implementation.
Figure Out Available Room
When planning a butchery, understanding the readily available space is essential, as it directly affects tools selection and process effectiveness. Companies must examine the overall square footage of the facility, including storage space, preparation, and display locations. This analysis needs to represent both straight and upright area, assuring ample area for tools such as meat saws, mills, and refrigeration systems. In addition, it is very important to consider the layout, consisting of gain access to points for shipments and consumer traffic circulation. This evaluation helps identify possible restrictions and confirms that all essential devices can fit easily without overcrowding. Effectively establishing available room will certainly assist in a much more well organized try these out and functional setting, eventually sustaining the butchery's operational demands and client experience.
Optimize Process Layout
To enhance process layout in a butchery, mindful factor to consider of area and layout is important, as these variables influence both efficiency and safety. An effective format reduces unnecessary activity, enabling personnel to perform tasks perfectly from getting to processing and product packaging. It is essential to assign certain areas for each and every phase of the butchering process, guaranteeing that tools and tools are conveniently accessible. Appropriate space ought to be designated for storage, refrigeration, and garbage disposal to maintain hygiene and enhance operations. In addition, safety methods have to be integrated right into the layout, offering clear pathways and emergency departures. By reviewing the room and maximizing the layout, a butchery can boost performance, lower threats, and ultimately enhance total service performance.
Research Study Brand Name Reputation
When picking butchery devices, comprehending brand name online reputation is vital. Sector leaders typically follow quality control criteria, which can substantially affect efficiency and integrity (Butchery Equipment). Evaluating a brand name's standing in the market can assist assure that the tools fulfills specialist expectations
Industry Leader Recognition
Industry leader acknowledgment plays an essential role in the butchery tools market, influencing buying decisions for numerous organizations. Business identified as sector leaders commonly have actually developed an online reputation for dependability, advancement, and consumer complete satisfaction. This recognition can originate from awards, accreditations, or testimonials from significant market figures. Purchasers tend to move in the direction of brands with a proven performance history, as these brand names are regarded to use remarkable products and solutions. In addition, industry leader recognition can enhance a company's reliability, making it much easier to build depend on with prospective clients. When choosing butchery tools, organizations should think about brands that have actually obtained accolades and recommendations, as these factors can significantly influence the total efficiency and long life of their tools financial investments.
Quality Control Standards
Recognizing sector leaders provides beneficial understanding into the relevance of quality control criteria in the butchery devices market. Respectable brands frequently adhere to stringent guidelines and certifications, ensuring their products satisfy high safety and performance criteria. This commitment to high quality not just instills consumer confidence yet also boosts the functional performance of butchers. Prospective purchasers need to look into brand track record by analyzing client evaluations and sector awards, which can work as indicators of integrity. On top of that, developed business usually purchase recurring item screening and advancement, guaranteeing their equipment remains competitive. By focusing on brand names that highlight quality guarantee, businesses can mitigate risks connected with tools failure and keep high standards in food security and processing.
Budget Intelligently
While selecting butchery equipment, mindful budgeting is crucial to guarantee lasting success and sustainability. Company owner need to evaluate their economic abilities and develop a practical budget plan that incorporates all necessary tools. Costs can vary significantly relying on the top quality and brand name of tools, so it is vital to prioritize crucial things while taking into consideration possible future needs.Investing in top quality tools may call for a greater preliminary investment but can result in financial savings out of commission and substitutes down the line. Additionally, site web discovering alternatives such as leasing equipment or purchasing used products can assist stretch budgets without giving up quality.A complete cost-benefit analysis is advisable to validate that each acquisition lines up with business's functional goals. By intending and allocating funds intelligently, services can avoid unforeseen costs that might impede growth and profitability. Ultimately, a tactical budget plan works as a foundation for an effective butchery procedure.
Look For Specialist Advice
Seeking specialist recommendations can greatly improve the decision-making process when selecting butchery devices. Market professionals, such as experienced butchers and equipment distributors, possess important understandings that can lead entrepreneur toward the most effective selections for their particular demands. Their experience can help identify crucial devices that maximizes efficiency and high quality while decreasing costs.Consulting professionals likewise home enables access to the most recent modern technology and developments in butchery equipment, ensuring that organizations continue to be affordable. In enhancement, they can use recommendations on upkeep and durability, assisting to stay clear of expensive mistakes down the line.Additionally, specialists can help in comprehending regional regulations and security requirements, which are vital for compliance. By leveraging professional expertise, entrepreneur can make informed decisions that line up with their functional objectives, inevitably bring about an extra successful and lasting butchery venture. Seeking such advice is a tactical financial investment in the service's future.
Often Asked Concerns
What Kinds of Meat Will I Mainly Be Handling?
Figuring out the sorts of meat to be refined is vital for any kind of butchery. This choice influences tools choice, operations performance, and general operational success, ensuring that the picked tools align with details meat handling demands.
How Typically Should I Maintain Butchery Tools?
The frequency of maintaining butchery devices mostly relies on use intensity. Routine evaluations, preferably every couple of weeks, guarantee optimal performance and safety and security, while deep cleansing and maintenance should occur quarterly to protect against potential malfunctions and expand equipment life-span.
Can I Purchase Used Equipment Rather Than New?
Purchasing used devices can be a practical choice, offering expense financial savings - Butchery Equipment. One must think about the condition, integrity, and required maintenance of the tools to ensure it fulfills functional standards and security requirements.
What Guarantees Are Typically Provided on Butchery Devices?
Guarantees for butchery equipment commonly range from one to five years, covering defects in products and handiwork. The specifics may differ by manufacturer, so it is a good idea to review guarantee terms before purchasing.
Are There Certain Accreditations for Butchery Tools?
The question of details certifications for butchery devices is essential. Usually, equipment may call for accreditations such as NSF or CE, guaranteeing compliance with safety and security and health requirements essential for food handling and processing atmospheres.